In the fast-paced world of reverse logistics, having efficient and standardized processes is essential. Setting up standard operating procedures (SOPs) not only brings order to the chaos but also ensures consistent performance and improved efficiency. From the proper handling of returns to the management of surplus inventory, having well-defined Standard Operating Procedures can streamline operations and reduce costs.

Key Takeaways:
1. Streamlined processes: SOPs help establish clear and standardized processes for handling reverse logistics operations, ensuring consistency and efficiency.
2. Improved quality control: SOPs enable the implementation of robust quality control measures, including inspection protocols and disposition criteria, to maintain product quality and customer satisfaction.
3. Enhanced accountability: Clearly defined roles and responsibilities in SOPs promote accountability among team members, reducing confusion and errors in reverse logistics processes.
4. Effective inventory management: SOPs guide inventory management practices, allowing for accurate tracking, categorization, and disposition of returned items.
5. Customer satisfaction: By providing clear instructions, prompt communication, and timely resolution, SOPs contribute to improved customer satisfaction in the reverse logistics process.
By implementing effective SOPs for reverse logistics, businesses can optimize their operations, reduce costs, improve customer satisfaction, and enhance overall efficiency in handling returned products.
Introduction to Standard Operating Procedures
In this article, we will explore the importance of setting up Standard Operating Procedures for reverse logistics and how they can benefit your business. We will delve into the key elements that should be included in these procedures and provide practical tips for implementation. Whether you are a retailer, manufacturer, or logistics service provider, this guide will help you understand the crucial steps needed to establish effective Standard Operating Procedures for your reverse logistics operations.
By implementing Standard Operating Procedures, businesses can minimize errors, reduce processing times, and optimize resource allocation. Moreover, documenting and standardizing processes can also lead to better training, knowledge sharing, and accountability within the organization.
Don’t let the complexities of reverse logistics overwhelm you. With the right set of Standard Operating Procedures, you can enhance operational efficiency and customer satisfaction while staying ahead in the competitive market.
Importance of standard operating procedures (SOPs) in reverse logistics
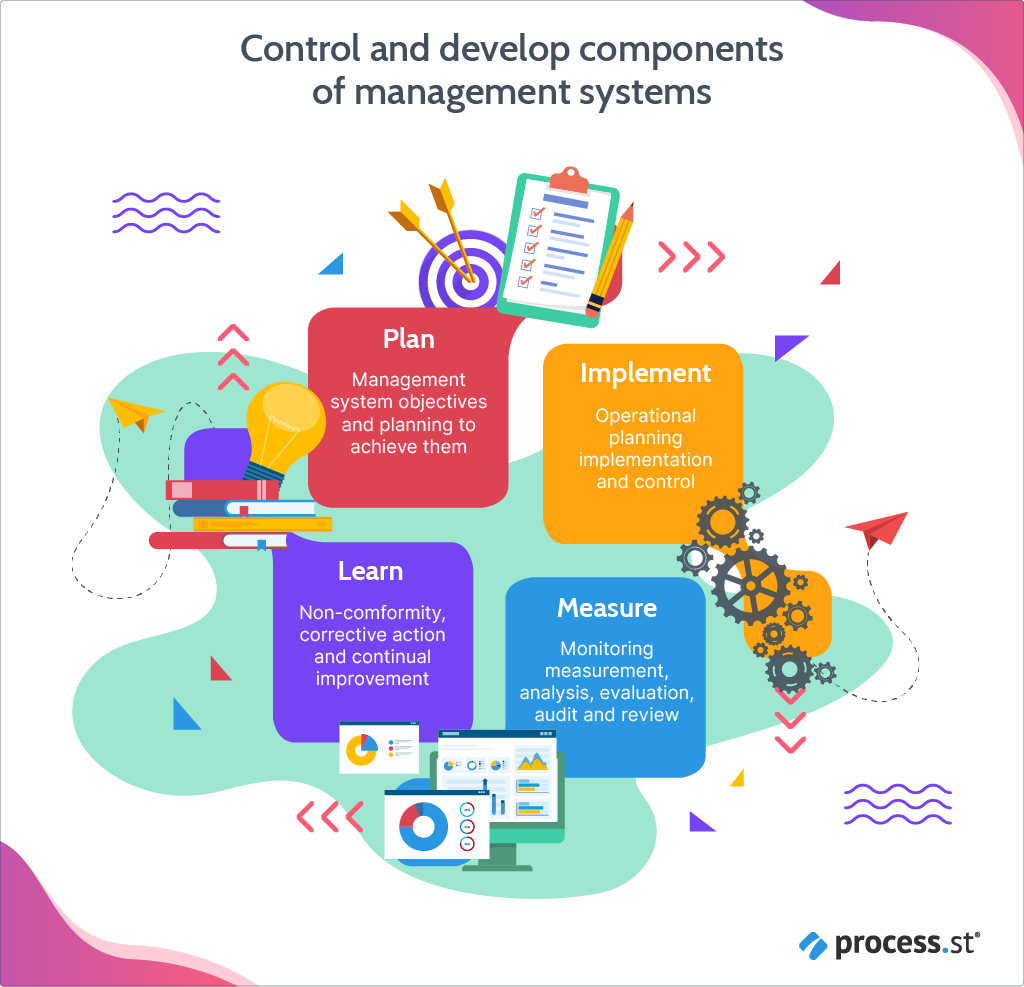
Reverse logistics, which involves the movement of products from the customer back to the manufacturer or retailer, can be a complex and challenging process. Without proper guidelines and procedures in place, businesses can face delays, errors, and unnecessary expenses. That’s where Standard Operating Procedures come in. They provide a roadmap for the entire reverse logistics process, ensuring that each step is carried out consistently and efficiently.
One of the key benefits of implementing Standard Operating Procedures in reverse logistics is the ability to minimize errors. With clear instructions and guidelines, employees can follow a standardized process, reducing the chances of mistakes and ensuring that each return or exchange is handled correctly. This not only improves customer satisfaction but also saves time and resources by avoiding the need for rework or additional processing.
Standard Operating Procedures also play a crucial role in reducing processing times. By defining the steps involved in receiving, inspecting, and documenting returned products, businesses can streamline their operations and expedite the resolution of customer issues. This not only improves efficiency but also helps organizations to meet customer expectations for prompt and hassle-free returns.
Moreover, documenting and standardizing processes can lead to better training, knowledge sharing, and accountability within the organization. New employees can be trained more effectively by following established Standard Operating Procedures, ensuring that they understand the proper procedures and expectations from day one. Standard Operating Procedures also provide a reference point for troubleshooting and resolving issues, allowing employees to share knowledge and best practices more easily. Additionally, having well-defined procedures creates a sense of accountability, as employees can be held responsible for following the established guidelines.
Key components of an effective SOP for reverse logistics
To create effective Standard Operating Procedures for reverse logistics, it is important to consider the key components that should be included. These components ensure that the procedures cover all necessary aspects of the reverse logistics process and provide clear guidance for employees to follow. Here are some key components to include in your Standard Operating Procedures:
1. Return Authorization Process: Outline the steps involved in obtaining authorization for returns, including the required documentation and any specific criteria for approval.
2. Receiving and Inspection: Define the process for receiving returned products, inspecting them for damage or defects, and documenting their condition.
3. Disposition: Specify the various options for handling returned products, such as refurbishment, repair, resale, or disposal, and provide guidelines for determining the appropriate course of action.
4. Inventory Management:
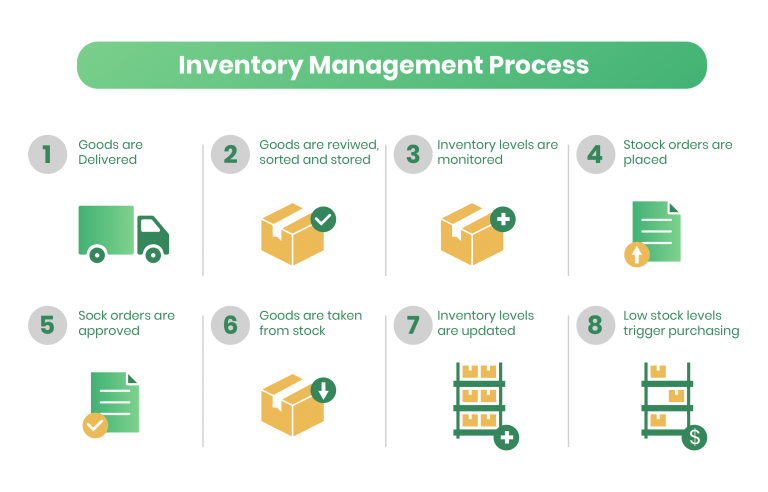
Detail the procedures for managing returned and surplus inventory, including tracking, storage, and disposal.
5. Data Analysis and Reporting: Explain how data collected during the reverse logistics process will be analyzed and reported, including metrics for measuring performance and identifying areas for improvement.
By including these key components in your Standard Operating Procedures, you can ensure that your reverse logistics operations are well-structured and efficient, minimizing errors and delays while maximizing customer satisfaction.
Step-by-step guide to creating Standard Operating Procedures for reverse logistics
Creating effective Standard Operating Procedures for reverse logistics involves a systematic approach that covers all aspects of the process. Follow these steps to develop comprehensive and actionable Standard Operating Procedures for your business:
1. Identify Process Steps: Start by mapping out each step involved in the reverse logistics process, from receiving returns to final disposition. Break down the process into smaller tasks to ensure that nothing is overlooked.
2. Document Procedures: For each process step, document the specific actions that need to be taken, including any required documentation, tools, or resources. Be clear and concise in your instructions, using bullet points or numbered lists for easy reference.
3. Assign Responsibilities: Identify the individuals or teams responsible for each process step and clearly communicate their roles and responsibilities. This ensures accountability and avoids confusion or duplication of efforts.
4. Define Performance Metrics: Establish key performance indicators (KPIs) to measure the success of your reverse logistics operations. This could include metrics such as processing time, customer satisfaction, and cost per return.
5. Test and Revise: Implement your Standard Operating Procedures on a small scale and gather feedback from employees involved in the process. Use this feedback to identify any areas for improvement and make necessary revisions to your procedures.
6. Train Employees: Provide comprehensive training to employees on the newly developed Standard Operating Procedures, ensuring that they understand the procedures and their role in the process. Regularly review and update training materials to keep employees informed of any changes or improvements.
By following these steps, you can create Standard Operating Procedures that are tailored to your specific reverse logistics operations and enable your business to operate more efficiently and effectively.
Best practices for implementing and maintaining Standard Operating Procedures in reverse logistics
Implementing and maintaining Standard Operating Procedures for reverse logistics requires a proactive approach to ensure their effectiveness and relevance over time. Here are some best practices to consider:
1. Regular Review and Update: Review your Standard Operating Procedures on a regular basis to ensure that they reflect current best practices and industry standards. Update them as needed to accommodate changes in your business processes or customer requirements.
2. Employee Feedback: Encourage employees to provide feedback on the Standard Operating Procedures and share their insights and suggestions for improvement. This promotes a sense of ownership and engagement, leading to better adherence to the procedures.
3. Continuous Training and Education: Provide ongoing training and education to employees to ensure that they stay up to date with the Standard Operating Procedures and any changes in the reverse logistics process. This can be done through regular workshops, refresher courses, or online training modules.
4. Monitoring and Measurement: Establish a system for monitoring and measuring the effectiveness of your Standard Operating Procedures. This can include regular audits, performance reviews, and customer feedback. Use this data to identify areas for improvement and make necessary adjustments to your procedures.
5. Communication and Collaboration: Foster a culture of communication and collaboration within your organization. Encourage employees to share their experiences and best practices related to reverse logistics, creating opportunities for learning and improvement.
By following these best practices, you can ensure that your Standard Operating Procedures remain relevant and effective, enabling your business to continuously improve its reverse logistics operations.
Common challenges in developing and implementing Standard Operating Procedures for reverse logistics
While implementing Standard Operating Procedures in reverse logistics can bring numerous benefits, there are also common challenges that businesses may face during the development and implementation process. Being aware of these challenges can help you anticipate and overcome them. Here are some common challenges:
1. Resistance to Change: Employees may resist adopting new Standard Operating Procedures, especially if they have been accustomed to working in a certain way. Overcoming this resistance requires effective communication, training, and a clear explanation of the benefits of the new procedures.
2. Complexity of the Process: Reverse logistics can be a complex process, involving multiple stakeholders and varying requirements. Developing Standard Operating Procedures that cover all aspects of the process can be challenging and time-consuming. Breaking down the process into smaller, manageable tasks can help simplify the development of Standard Operating Procedures.
3. Lack of Resources: Developing and implementing Standard Operating Procedures requires time, effort, and resources. Limited resources, such as staffing or technology, can hinder the development and implementation process. Prioritizing and allocating resources effectively can help overcome this challenge.
4. Maintaining Consistency: Ensuring consistent adherence to Standard Operating Procedures can be a challenge, especially in a dynamic and fast-paced environment. Regular training, monitoring, and feedback are essential to maintain consistency and identify areas where improvements are needed.
By anticipating these challenges and addressing them proactively, businesses can successfully develop and implement Standard Operating Procedures that enhance their reverse logistics operations.
Case studies: Successful implementation of Standard Operating Procedures in reverse logistics
To understand the real-world impact of implementing Standard Operating Procedures in reverse logistics, let’s explore a few case studies of businesses that have achieved success through standardized processes:
1. Company X: Company X, a leading e-commerce retailer, implemented Standard Operating Procedures for their reverse logistics operations, including return authorization, inspection, and inventory management. As a result, they were able to reduce processing times by 20%, improve customer satisfaction, and reduce costs associated with returns.
2. Company Y: Company Y, a manufacturer of electronic devices, developed Standard Operating Procedures for their refurbishment process. By standardizing the steps involved in refurbishing returned products, they were able to increase productivity, reduce errors, and improve the quality of refurbished products.
3. Company Z: Company Z, a logistics service provider, implemented Standard Operating Procedures for their entire reverse logistics process, from receiving returns to final disposition. This enabled them to optimize resource allocation, reduce processing times, and provide their clients with accurate and timely reporting on returned products.
These case studies highlight the positive impact of implementing Standard Operating Procedures in reverse logistics, demonstrating how standardized processes can lead to improved efficiency, cost savings, and customer satisfaction.
Tools and software for managing SOPs in Reverse Logistics
Managing Standard Operating Procedures for reverse logistics can be made easier with the help of various tools and software. These tools provide a centralized platform for creating, storing, and updating Standard Operating Procedures, as well as tracking their implementation and effectiveness. Here are some tools and software options to consider:
1. Document Management Systems: Platforms such as Google Drive, Microsoft SharePoint, or Dropbox provide a secure and organized way to store and share Standard Operating Procedures with relevant stakeholders. These systems allow for version control, ensuring that everyone has access to the most up-to-date procedures.
2. Workflow Management Software: Tools like Trello, Asana, or Monday.com can help manage the implementation and execution of Standard Operating Procedures by providing task management, collaboration, and progress tracking capabilities. These platforms enable real-time visibility into the status of each process step and promote accountability.
3. Process Mapping Software: Tools like Lucidchart or Microsoft Visio can be used to visually map out the reverse logistics process and create flowcharts or diagrams that illustrate the steps involved. These visual representations make it easier to understand and communicate the procedures to employees.
4. Training and Learning Management Systems: Platforms like TalentLMS or Moodle can be used to create and deliver training materials related to the Standard Operating Procedures. These systems allow for the creation of interactive training modules, quizzes, and assessments to ensure that employees understand and adhere to the procedures.
By leveraging these tools and software, businesses can effectively manage their Standard Operating Procedures, streamline their reverse logistics operations, and ensure consistent adherence to established procedures.
Training and education for reverse logistics SOPs
Implementing Standard Operating Procedures in reverse logistics requires comprehensive training and education for employees at all levels. Providing the necessary knowledge and skills ensures that employees understand the procedures and can effectively carry out their responsibilities. Here are some training and education strategies to consider:
1. Orientation and Onboarding: Incorporate reverse logistics SOP training into the orientation and onboarding process for new employees. This ensures that they receive the necessary training from the start and understand the importance of adhering to the established procedures.
2. Role-Specific Training: Tailor training programs to specific roles within the reverse logistics process. This allows employees to focus on the procedures relevant to their responsibilities and ensures that they have a deep understanding of their role in the overall process.
3. Hands-on Training: Provide hands-on training opportunities, such as simulations or real-life scenarios, to allow employees to practice following the Standard Operating Procedures in a controlled environment. This helps build confidence and familiarity with the procedures.
4. Ongoing Education: Offer continuous education opportunities to keep employees up to date with changes in the reverse logistics process and any updates to the Standard Operating Procedures. This can be done through workshops, webinars, or online training modules.
5. Knowledge Sharing: Encourage employees to share their experiences and best practices related to reverse logistics Standard Operating Procedures. This can be done through regular team meetings, knowledge-sharing sessions, or online collaboration platforms. Creating a culture of learning and sharing promotes continuous improvement.
By investing in training and education for reverse logistics Standard Operating Procedures, businesses can ensure that employees have the necessary skills and knowledge to execute the procedures effectively, leading to improved operational efficiency and customer satisfaction.
Conclusion
As the world of reverse logistics continues to evolve, the importance of standard operating procedures (Standard Operating Procedures) cannot be overstated. By implementing Standard Operating Procedures, businesses can minimize errors, reduce processing times, and optimize resource allocation. Moreover, documenting and standardizing processes can also lead to better training, knowledge sharing, and accountability within the organization.
With the complexities of reverse logistics, having well-defined Standard Operating Procedures is crucial for businesses to enhance operational efficiency and customer satisfaction while staying ahead in the competitive market. By following the steps outlined in this guide, businesses can create effective Standard Operating Procedures tailored to their specific reverse logistics operations and overcome common challenges in their development and implementation.
The future of Standard Operating Procedures in reverse logistics lies in their continuous improvement and adaptation to changing business needs and customer expectations. By regularly reviewing and updating Standard Operating Procedures, leveraging tools and software, and investing in training and education, businesses can ensure that their reverse logistics operations remain efficient, cost-effective, and customer-centric.
Don’t let the complexities of reverse logistics overwhelm you. With the right set of Standard Operating Procedures, you can navigate the challenges, optimize your processes, and achieve success in your reverse logistics operations. Start implementing Standard Operating Procedures today and position your business for a brighter future in the world of reverse logistics.
Check for our previous blog post by clicking here: